How To Make An Acoustic Wall Panel
For the purpose of reducing the echo in my home when recording audio, I made some DIY acoustic panels. This project is an excellent and reasonably priced way to create your own acoustic panels if you’re want to lessen the noise in your room! And these acoustic panels work effectively.
You may soundproof your home studio by creating your own acoustic panels using the instructions in this guide.
In this article, I will share my experience How to make an acoustic wall panel?
How To Make An Acoustic Wall Panel?
You can create your own acoustic wall panels at low cost. The directions, and specs for very effective acoustic panels are provided below.
The fundamental components of an acoustic panel are as follows:
- An acoustically transparent cloth cover that makes nice look of your panel.
- The material that absorbs sound, it will performs the acoustical work to reduce echoes.
- A robust wood framework to fix the panel on wall.
Let me guide you step by step!
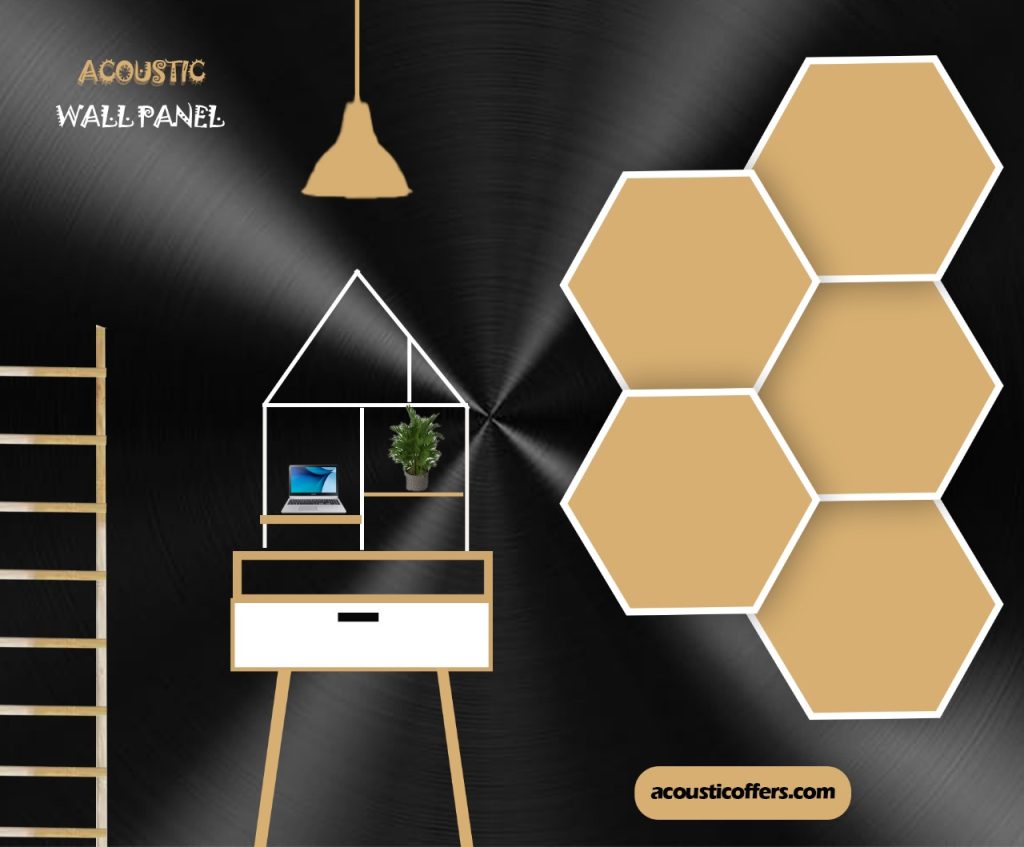
Steps To Create An Acoustic Wall Panel:
Step 1: Choose an acoustic core material
The following qualities must be present in the acoustic core material:
- Board insulation made of mineral fibers or dense fiberglass
- It should be Uniface
- Its density should be 6 to 8 pounds per cubic foot.
- Its thickness should be 2 or 3 inch.
Two acceptable material options include:
- $1.00 per square foot
- $3.00 per square foot
Insulation made of fiberglass and mineral fibers is known to irritate. When working with the insulation, kindly don a mask, gloves, and eye protection. For safe use, adhere to the manufacturer’s instructions.
Step 2: Create a wooden frame to enclose each panel
I used a furring strip for the wood frame, which is affordable and accessible at any hardware or timber supply. The panel’s face should be completely flat. Make sure each strip is straight and doesn’t have any noticeable wood missing by carefully inspecting it.
- Cut two furring strip segments to 49-3/8″ and two segments to 24″ for each panel frame. To guarantee a tight fit around the insulation, measure and cut accordingly.
- Place the insulation in such a way that the panel’s bottom face is flat and parallel to the wood frame.
- Spray a significant amount of adhesive all over the insulation’s perimeter. Glue will secure the insulation inside the frame.
- Set up pieces of wood all around the fiberglass panel. The insulation should be compressed only a little bit by the frame when it is secured snugly around it.
- To assure alignment and stop the board from splitting, drill a pilot hole before cutting the wood in one corner. For each corner, you should follow the same step. Now apply wood glue. After that connecting wood pieces by using screws.
- Spray adhesive and wood glue should be given 24 hours to dry.
Step 3: Pick a fabric that transmits sound, then wrap the panel in it.
The cloth cover’s main function is to give the panel a classy, attractive appearance. You must make sure that your fabric is acoustically transparent in order to ensure that sound passes through to your fiberglass insulation.
Holding the fabric to your mouth and exhaling through it is an easy way to check this. There will be some airflow resistance through the fabric that you can feel. Pick a substance that offers very minimal resistance. For this use, solid vinyl, leather, or cloth with an acrylic backing are not acceptable.
Stretching your panel using fabric:
- 65″ length fabric should be laid out face down on the ground. On the surface of the fabric, put your framed panel with the flat, level, or even side pointing up.
- The cloth should be wrapped around the panel’s backside and nailed to the timber frame every 3″ on one of the corners.
- Continue down the panel edge at 3″ intervals, pulling the cloth taut along the other edge, and staple. On the panel reverse side, spray glue below any leftover patches of loose cloth.
Step 4: Attach the panel to your ceiling or wall.
These panels can be placed in the same way as a large piece of art. To ensure the stability, safety, and security of your panel, use your judgment and discretion.
You can now fully appreciate your home theater or music collection. The majority of people are shocked by how well-treated acoustics make music and movies sound.
Costs of Materials and Tools
In order to save money by doing it yourself, you’ll need to build a few acoustic panels. The cost-effectiveness of building panels over purchasing pre-made ones increases as you make more of them.
When comparing store-bought panels, it’s important to consider shipping expenses. The cost of shipping might nearly treble, based on how many panels you purchase.
FAQs (Frequently Ask Questions)
What kind of material works best for acoustic panels?
It would be suitable to use a thin, polyester imitation linen that would keep the pattern and color remarkably well. Muslin is another alternative for acoustic fabric because it is relatively breathable but is sufficiently tightly woven to prevent visibility of the internal panel and components.
What is the core material of a wood wall acoustic panel?
Although 6 pcf fiberglass is generally used to make acoustic absorption panels, other materials including recycled polyester, concrete mixture wood fiber, pierced wood, and perforated wood can also be used.
What materials can absorb sound?
Varying from acoustic ceiling panels, glass panels, suspension ceiling panels, nylon wool, rock wool, and fiberglass foam. One thing unites all of these remedies: they all absorb sound. This is due to the open-celled nature of all these materials.
Does fabric reduce sound?
Yes fabric can reduce sound. The polished surfaces echo, which is frequently perceived as an unpleasant sound. Fabrics can be used to combat this. They take in the sound and lessen noise pollution as a result. Additionally, they can enhance the room’s acoustics and enhance communication.
How thick should acoustic panels be?
3 inch thick acoustic foam will assist absorb high, mid, and low end frequencies. The 2″ thick profile is the most common and a safe pick for anyone planning a DIY vocal booth, studio, home theater, practice room, or a broadcasting location.